What is Absorption Costing?
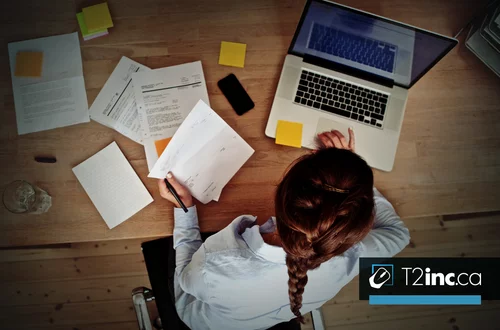
Absorption costing, also known as absorption accounting, full cost (FC) accounting, or full costing, is an essential tool in corporate financial management. It is an accounting method that allows companies to precisely calculate the full cost of a product or service, including all expenses associated with its manufacture and marketing. Using this analytical approach, businesses can set competitive sales prices, assess company profitability and make informed decisions.
In this guide, our corporate accounting experts show you how absorption costing can be used to calculate full cost, by allocating direct and indirect costs using cost centres and work units.
Understanding how absorption costing works
Full costing is one of several cost accounting methods used to calculate the cost of a company's products or services. Defined as the sum of all expenses related to the manufacture and marketing of a product, full costing provides an overall view of expenses incurred.
Accurate costing is essential for setting competitive selling prices on the market. By understanding the various components of cost in detail, companies can make objective and strategic decisions based on whether a product or service is profitable.
When it comes to setting a selling price, it’s important to consider direct costs (raw materials, direct labor, etc.) and indirect costs (overheads, administrative costs, etc.).
Types of costs in absorption accounting
Distinguishing between a company's direct and indirect costs helps us understand how different expenses are allocated to products or services.
Direct costs
Direct costs can be directly attributed to a specific product or service. They generally include raw materials and labor required for production.
Direct costs are relatively simple to allocate. For example, if you manufacture furniture, wood and nails are direct expenses, as are the hours worked by the craftsmen who make the furniture.
Indirect costs
Indirect expenses, on the other hand, are costs that cannot be directly attributed to a specific product or service. They are usually part of the company’s overhead costs, such as administration, advertising, rent or other general expenses related to running the business.
Breakdown of overhead costs
To allocate indirect costs accurately, absorption costing relies on cost centers. Cost centers are groupings of expenses corresponding to homogeneous activities within the company. They may be procurement centers, production or transformation centers, distribution centers or other relevant groupings depending on the company's activity.
Once indirect expenses have been grouped into cost centers, they are further divided using allocation keys. For example, to allocate advertising costs, we could use the share of sales generated by each product or service. Similarly, to allocate rent costs, we could use the surface area occupied by each activity center.
Thanks to cost centers, companies can obtain a more accurate view of the real costs of their products or services. As a result, they can better assess each product’s profitability, and make better decisions about pricing, resource optimization, budgets, etc.
Absorption costing: the complete calculation
Once direct and indirect costs have been allocated, it is possible to calculate the full cost of a product or service. The formula for calculating full cost is: full cost = direct costs + indirect costs.
In absorption costing, it is also important to correctly value inventories of raw materials and finished goods to get an accurate picture.
Example of absorption costing
Let's take the example of a company that manufactures wooden furniture. To determine the cost of a piece of furniture, the company uses absorption costing.
- Allocation of direct expenses: The company identifies the direct expenses associated with furniture production, such as the cost of wood and direct labor. These expenses are easily attributed to the product, as they are specific to its manufacture.
Let's assume that the cost of the wood used for a piece of furniture is $200 and the craftsmen's direct labor time for its manufacture is 10 hours billed at $20 per hour.
- Allocation of overhead costs: The company also has indirect expenses that cannot be directly attributed to a specific product. These include overheads such as administrative salaries, rent, advertising costs, etc.
To allocate these overheads, the company creates cost centers, such as the production center and the administrative center. Overheads are then allocated to these centers according to an allocation key, such as the proportion of labor costs or the surface area occupied by each center.
Let's assume that the company's total overheads amount to $5,000, and that the primary allocation assigns 60% to the production center and 40% to the administrative center.
- Determine work units: To allocate overheads to each piece of furniture, the company uses work units that represent the contents of the cost centers. In our example, the work unit for the production center is the number of hours of direct labor, and the work unit for the administrative center is the number of pieces of furniture produced.
If the production center has worked 1,000 hours to manufacture the furniture, and the company has produced 100 pieces of furniture, we obtain labor units of 1 hour of direct labor and 10 pieces of furniture.
- Calculating the full cost: Using the information gathered, the company can now calculate the full cost of a piece of furniture. The direct cost of the furniture is the sum of direct expenses: $200 for wood + (10 hours x $20/hour) = $400.
For indirect costs, the company allocates a share of indirect costs to each work unit. In our example, the indirect cost per hour of direct labor is 60% of $5,000/1,000 hours = $3 per hour. The indirect cost per piece of furniture is 40% of $5,000/100 pieces = $20 per piece.
Thus, the full cost of a piece of furniture would be $400 (direct cost) + $30 ($3 x 10 hours) + $20 = $450.
By using the full cost method, this company can accurately estimate the cost of each piece of furniture and set a competitive selling price that takes into account all the costs incurred in the production process.
Improve your company's financial management with T2inc
Absorption costing offers a number of business advantages, including a better, more accurate understanding of costs, the potential to make informed decision-making and the means to optimize resources to improve profitability.
T2inc corporate accounting and taxation specialists understand the importance of absorption costing and know how to put it into practise.
Call T2inc for help implementing absorption costing within your company, and achieve concrete results in your company's financial management.
Contact our experts
Have a question? Need help? Fill out our online form to get help from our experts.
Contact usNeed more help?
Contact us by filling out our form
Are you interested in our services, but would like more information before taking the plunge? Contact us today and one of our tax accountants will be in touch to help you.
At T2inc.ca, we're committed to helping business owners manage their company's tax affairs so they can grow their business.