What is Activity Based Costing?
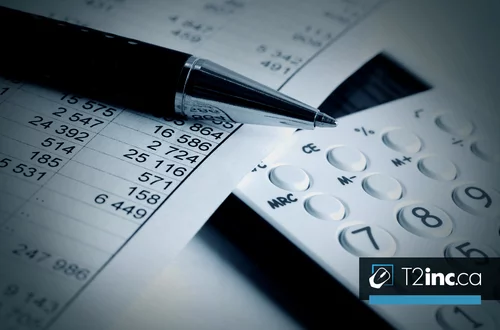
In an increasingly competitive corporate environment, companies must constantly find ways to get an edge. Effective cost management plays a crucial role in top business performance. This is where the ABC method comes in.
As a specialist in business accounting, T2inc understands the importance of accurate cost management in optimizing our clients' profitability. Here we explain activity based costing in detail, so that you can understand how it works and the benefits it can bring to your business.
What is the ABC method?
Activity based costing, or ABC, is a variant of full costing (also called absorption costing). ABC is an approach to cost management that enables costs to be analyzed and allocated more precisely, based on the activities or processes within a company.
ABC aims to provide a more accurate and detailed understanding of the costs associated with different products, services, or processes. Unlike traditional costing methods, which often focus on products or departments, the ABC method focuses on the specific activities that generate these costs.
A fundamental principle of the ABC method is choosing to categorize activities according to their strategic importance or value to the company. Rather than treating all activities as equivalent, the ABC method recognizes that certain activities have more or less impact on the company's operations.
To quantify and allocate costs accurately, the ABC method uses cost drivers. Cost drivers are measures or key performance indicators that link activities to the costs they generate. These drivers can be based on physical quantities, such as production time or number of orders, or on financial measures, such as sales generated or sales volume.
By using appropriate cost drivers, the ABC method provides a detailed view of cost distribution, enabling companies to make more informed decisions on cost management and profitability.
Advantages of the ABC method
When correctly implemented, the ABC method offers several significant advantages to company cost management. Let’s take a closer look.
Greater precision
The ABC method precisely attributes costs to specific elements of business operations, such as products, services, customers, etc. This is an advantage because it allows analysts to use appropriate cost drivers to focus on specific activities and more accurately assess costs associated with each activity.
In turn, businesses can clearly understand the exact quantity of company resources consumed by each element. They can determine which costs are more or less important to the company’s success, rather than simply dividing costs into broader, more arbitrary categories.
Informed decision-making
By better understanding the costs associated with each activity, product, service, or customer, decision makers can identify sources of high costs, unprofitable activities, or process inefficiencies. As a result, they can implement targeted optimization strategies and make more informed decisions to improve the profitability and sound management of their business.
Steps to implement the ABC method
To implement the ABC method, you will need to follow several steps.
1. Identify key activities
The first step is to identify your company's key activities. This involves breaking down all company operations into distinct, homogeneous groups. These could include production, inventory management, distribution, customer service, etc. The aim is to identify all activities that have a significant impact on your company's overall costs.
2. Choose appropriate cost drivers
Once key activities have been identified, you need to choose appropriate cost drivers to quantify them. It's important to select relevant cost drivers so that you can accurately measure the resource consumption of each activity.
3. Allocate resources to activities
Once you have defined relevant cost drivers, it's time to analyze each activity and determine the quantity of resources it consumes (material, human, financial, etc.). This step allows you to link costs to activities, based on the cost drivers you selected earlier.
4. Group cost drivers and calculate unit costs
Once resources have been allocated to activities, similar cost drivers can be grouped together according to shared characteristics, to simplify cost calculation. For each group, you'll need to calculate the unit cost associated with each cost driver. This involves dividing the total cost of the group by the number of cost drivers it uses.
5. Determine the cost of each activity
Finally, by combining resource costs and driver costs for each activity, you'll get a precise view of the costs associated with each specific activity in your business.
Example of how to use the ABC method
Let's take the example of a furniture manufacturing company wishing to analyze and optimize its costs using the ABC method. The company identifies its three key activities: material cutting, furniture assembly and finishing.
- Identification of the company's key activities:
- Material cutting: activity required to transform raw materials into furniture parts
- Furniture assembly: assembling cut pieces to create finished furniture
- Finishing: applying finishes, such as paint or varnish, to the assembled furniture
- Choice of appropriate cost drivers:
- For cutting materials: the number of cutting hours required for each piece of furniture
- For furniture assembly: the number of man-hours required for each piece of assembled furniture
- For finishing: the number of man-hours required for each piece of finished furniture
- Allocation of resources to activities:
- Material cutting: 500 man-hours per month, for a monthly cost of $10,000
- Furniture assembly: 800 man-hours per month, for monthly cost of $15,000
- Finishing: 300 man-hours per month, for monthly cost of $6,000
- Grouping of inductors and calculation of unit cost per driver:
- Material cutting: $10 per hour of cutting
- Furniture assembly: $18.75 per hour of labor
- Finishing: $20 per hour of labor
- Activity based costing:
For a piece of furniture requiring 2 hours of cutting, 4 hours of assembly and 1 hour of finishing, the associated costs would be as follows:- Material cutting: 2 hours x $10/hour = $20
- Furniture assembly: 4 hours x $18.75/hour = $75
- Finishing: 1 hour x $20/hour = $20
Thus, the total cost for this specific piece of furniture would be $115.
T2inc can provide business accounting advice
The ABC method is a powerful tool for corporate cost management that offers significant benefits including accurate cost allocation, better cost understanding and resource optimization. By working with T2inc, you can take full advantage of the benefits of the ABC method to optimize your corporate cost management and boost your company's profitability.
Our team of experts can advise you on identifying key activities and selecting appropriate cost drivers. Contact T2inc today to find out how our expertise in corporate accounting and taxation can help you.
Contact our experts
Have a question? Need help? Fill out our online form to get help from our experts.
Contact usNeed more help?
Contact us by filling out our form
Are you interested in our services, but would like more information before taking the plunge? Contact us today and one of our tax accountants will be in touch to help you.
At T2inc.ca, we're committed to helping business owners manage their company's tax affairs so they can grow their business.